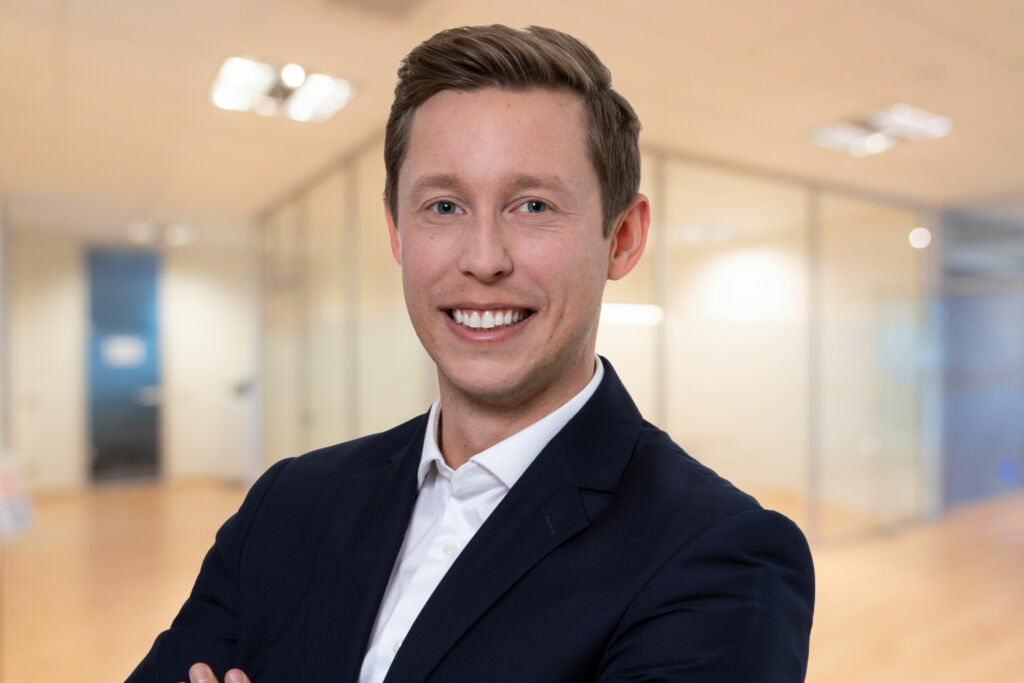
Die These ‚Daten sind das neue Öl.‘ wurde im Jahr 2017 erstmals im Magazin ‚The Economist‘ formuliert. Doch wurden daraus auch auf dem OT-Shopfloor der automatisierten Produktion Konsequenzen daraus gezogen? Diese Frage ist von großer Bedeutung, zumal etwa der Fachkräftemangel, zunehmender Margendruck und unsichere Lieferketten die Anforderungen an Effizienz und Funktionsfähigkeit von automatisierten Produktionsstraßen immer weiter steigen lassen. Wer nach Effizienz strebt, sollte Prozessschritte auf den Prüfstand stellen und optimieren sowie Produktionsausfälle entlang aller Dimensionen vermeiden.
Data Management und Data Governance
Hier kommen Data Management und Data Governance ins Spiel: Nur wer etwas messen, darstellen und verstehen kann, kann es auch verbessern. Zudem setzen alle technologischen Zukunftsthemen der Industrie 4.0 ein Data-Governance-Fundament voraus. Dabei ist die Etablierung eines konsistenten Datenmanagement-Prozesses für Einstellungen und Änderungen an den Maschinen wie auch für die physischen Assets selbst mehr als eine Maßnahme zur Kostenersparnis. Sauberes und zuverlässiges Data Management zur Unterstützung des Recovery Prozesses kann die Produktivität erhöhen – und ist ab Oktober 2024 auch eine regulatorische Anforderung, die im Rahmen der NIS2-Direktive (Network and Information Security Directive) in Kraft treten wird.
Wie eine Strategie aussehen kann
Aber wie kann eine konkrete Vorgehensweise aussehen, mit der Unternehmen diesen Anforderungen gerecht werden? Oft sind IT-Manager versucht, bereits etablierte Muster und Lösungen wie Asset und Data Management aus der IT-Welt 1:1 in die Welt der OT zu transferieren. Die beiden Ebenen sind jedoch zu unterschiedlich. Für IT-Manager ist die wichtigste Dimension Cybersicherheit. Zwar ist dieser Aspekt auch in der OT relevant, doch gelten auf dem Shopfloor andere Prioritäten. Dort sind die wichtigsten Maximen Uptime und Produktionsdauer. Jede Stunde Downtime verursacht Kosten. Gleichzeitig sind viele OT-Netzwerke nahezu hermetisch von der Außenwelt abgeriegelt, insbesondere dem öffentlichen Internet. Daher sind sowohl Netzwerke als auch Protokolle in der OT und der IT sehr unterschiedlich voneinander aufgesetzt. Das Manufacturing Execution System (MES) HYDRA optimiert Produktionsprozesse für Fertigungsunternehmen, um Wettbewerbsvorteile zu erzielen. ‣ weiterlesen
MES-Integrator und 360-Grad-Partner für optimierte Fertigung
Schon Katalogisierungen können zum Ausfall führen
Wo es in der IT ausreicht, eine Asset-Liste anhand der im Netzwerk verbundenen und über IP-Adressen identifizierbaren Geräte zu erzeugen, zeichnen sich OT-Netzwerke durch heterogene Kommunikationsprotokolle und hochsegmentierte Netzwerke aus. Sehr alte Geräte in der Produktion könnten sogar bereits durch einen Netzwerkscan abzustürzen. Im Worst Case kann eine simple Katalogisierung zum Stillstand führen. Hinzu kommt, dass Optimierungsanstrengungen eine weitere Komplexitätsebene erzeugen.
SPS-Anpassungen bleiben oft schlecht dokumentiert
Viele oft nicht vernetzte und heterogene PLCs (Programmable Logic Controller, speicherprogrammierbare Steuerungen) werden von internen und externen Mitarbeitern laufend angepasst und optimiert. Die sich daraus ergebende Änderungshistorie ist oft schlecht oder gar nicht dokumentiert, der Änderungsprozess unterliegt allenfalls geringer Governance. Hier müssen Unternehmen oft nachsteuern.
Kein manuelles Datenmanagement
In der Praxis greifen Unternehmen manchmal auch auf Behelfslösungen zurück. So werden Änderungshistorien mit Excel getrackt oder Projektdaten auf einem USB-Stick gespeichert. Von einer Integration von IT und OT kann vielerorts nicht die Rede sein. Doch Bereits die Menge der Daten, die auf einem modernen Shopfloor entstehen zeigt: Manuelle Erfassung, Analyse und Wiederherstellung kann nicht mehr die Lösung sein. Hier kann ein übergreifendes Data-Management-System helfen, das kontinuierliche Backups aller Ist-Zustände der Maschinen und Systeme innerhalb der Produktionsumgebung erfasst sowie Daten zu physischen Assets ausliest und im Asset-Management verwaltet.
Bei Alarmen greifen Menschen ein
Der Mensch kommt erst wieder ins Spiel, wenn es um die Interpretation der erfassten Daten geht, oder wenn die Software bei ungeplanten Änderungen außerhalb des definierten Workflows Alarm schlägt. Und damit schließt sich der Kreis zur Cybersicherheit. Denn auf Basis der aufbereiteten Daten lassen sich wiederum Common Vulnerabilities and Exposures (CVEs) identifizieren und auch ein Obsolescence Management realisieren.
Kosten gespart, Basis für mehr
Beim Aufsetzen eines Data-Governance-Prozesses in der OT bildet das Sammeln relevanter Informationen in einem zentralen Repository die Basis für die erfolgreiche Konvergenz von IT und OT. Daraus ergeben sich drei Effekte: direkte operative Kosteneinsparungen beim Arbeitsaufwand im Datenmanagement-Prozess, Einsparungen durch die Vermeidung bzw. starke Verkürzung von Downtimes durch regelmäßige, zentral verfügbare Backups und mehr Kapazitäten in den verantwortlichen Abteilungen, um die Grundlage für den Ausbau neuer Use Cases rund um KI, Big Data oder Predictive Maintenance zu legen.